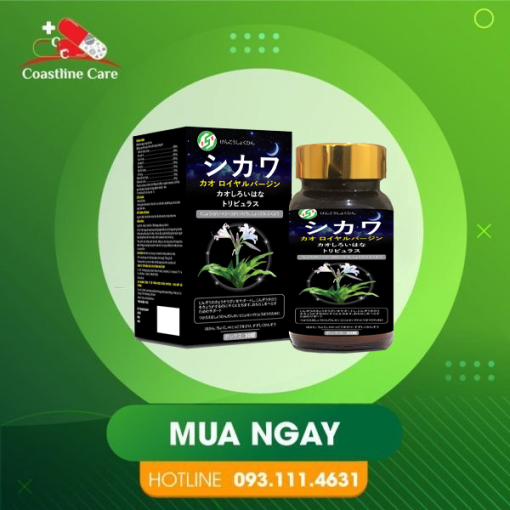
Be as certain as you possibly can when defining your difficulty. It can make it simpler to detect root causes afterwards.
This area desires additional citations for verification. Remember to enable make improvements to this post by including citations to reputable sources in this segment. Unsourced content may very well be challenged and eradicated. (June 2023) (Learn the way and when to get rid of this information)
Cost - What are the monetary inputs of the procedure, and What exactly are the economic outputs of the process?
The scientific process might be integrated into RCA by using cycles of PDCA. The planning phases encompass describing the trouble, collecting facts, and forming a speculation.
You can even utilize the scientific technique in the shape from the well-identified plan-do-Examine-act (PDCA) cycle to empirically look into the failure. Typically, failure investigations begin with brainstorming possible brings about and listing them within an Ishikawa diagram. This is not essentially Incorrect, but generally the ideas detailed don't lead into the failure below investigation.
Ascertain root results in: Use five Whys to breakdown each from the prioritized will cause further right up until you get to the root bring about (approach breakdown). Just take Action: Use the insights attained to develop alternatives or action strategies to deal with the foundation will cause determined.
Learn the way to employ an Ishikawa diagram to boost top quality Handle. Learn just what the 6Ms are inside the Ishikawa diagram and a lot more.
Measurement - Are methods of measurement and Handle correct and precise. Do they should be altered?
Just about every item from the Ishikawa diagrams must be viewed for a speculation that might demonstrate the cause of the failure less than investigation. A very good speculation must be uncomplicated and general though keeping away from producing a lot of assumptions and may have the ability to nha thuoc tay make refutable predictions. An easier speculation is more very likely to be correct.
Every single lead to or cause for imperfection is a source of variation. Results in are often grouped into main groups to discover and classify these sources of variation.
Also referred to as a Trigger and Effect diagram, or Ishikawa diagram. The method was established by Kaoru Ishikawa inside nha thuoc tay the 1960’s. He created it to assist workforce stay clear of remedies that just deal with the signs and symptoms of a much bigger dilemma.
They resemble a fish skeleton, Along with the "ribs" representing the brings about of the occasion and the ultimate end result showing up at the head of your skeleton. The objective of the Ishikawa diagram is to permit management to pick which difficulties need to be tackled so that you can acquire or prevent a particular function.
Detect Big Groups: Attract quite a few diagonal lines (the ribs) branching off within the spine. Use Shikawa the 6 M’s or four P’s from earlier mentioned as a place to begin, but feel free to change them as necessary to your procedure and predicament.
Other typical uses with the Ishikawa diagram contain using it like a methodology for creating product or service patterns that solve realistic difficulties. It can also be Utilized in quality defect avoidance to identify likely elements resulting in an General impact.